Personal Protective Equipment (PPE) is important in protecting people from injuries, as long as they use them according to their guidelines. Since improving employee safety is always an important concern, the use of PPE tracking RFID tag has become prevalent in many industries worldwide now.
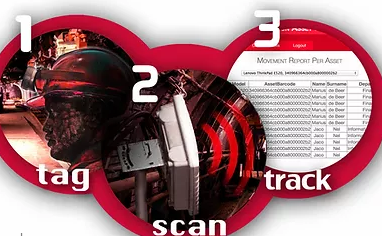
PPE Tracking RFID Tag Management
One of the reasons people become injured at the workplace is because they weren’t using PPE or they were using it incorrectly. The reason some people don’t use PPE is because they don’t have quick and easy access to it when it’s needed. Often times, this is because they are unable to find what they need. In trying to save time, they take a risk, and end up paying the price. In turn, they lose work, the company needs to bring in a replacement, and worker’s compensation claims need to be filed. RFID is a simple solution to a potentially huge problem.
How PPE tracking RFID tag Works
RFID tags are embedded into PPE items. With every item tagged, they can be entered into an asset tracking Management system for tracking.
When someone needs PPE, they can find it easily because the tracking system identifies its current location. A simple checkout process identifies who’s using the equipment and when they signed it out. When removed from the PPE storage area, an RFID antenna will register the transaction in the system.
After it’s used, the equipment’s RFID tag is scanned again when it’s brought back to the storeroom, and the system notes its updated status and location.
Tracking Purpose
With the RFID scanned with each use, it’s possible to see when an item is being used, where it’s being used, who used it, and when it’s being returned. All information is stored on the cloud, and reports can be generated from that data.
Tracking Repairs and Replacements
For it to function properly, PPE needs to be kept in optimal condition. Many types of protective equipment need to be routinely inspected, maintained, and (if necessary) replaced. With an RFID-based warehouse management system, determining which items are out for repair, or if a replacement is on its way, is quick and simple.
PPE Tracking RFID Tag Management
Organizations have been fined because of not having adequate PPE. Employees who have become injured have sued their employers because of problems with access and use of items. Don’t put your organization at risk for noncompliance with safety regulations, and don’t face legal trouble because of it. RFID offers a quick, easy solution for managing your PPE items effectively.
The versatility, speed, and accuracy of RFID makes the RFIDHY tracking solution a sure win for PPE management. The system can also be easily tailored to support Vendor Managed Inventory (VMI), which is popular among PPE manufacturers and distributors. It offers peace of mind like no other system on the market. We can help you understand how to use RFID tags on PPE items, how to enter them into a system that will track them wherever they go, and whenever they are used.
We RFIDHY supply hardware (PPE Tracking RFID Tag, RFID reader etc.) for PPE RFID solution, we are warmly welcome software and integrate company all over the world contact us for future cooperation.